① 刃先のチェック
チップや刃先、台金の破損状態をチェックする工程です。
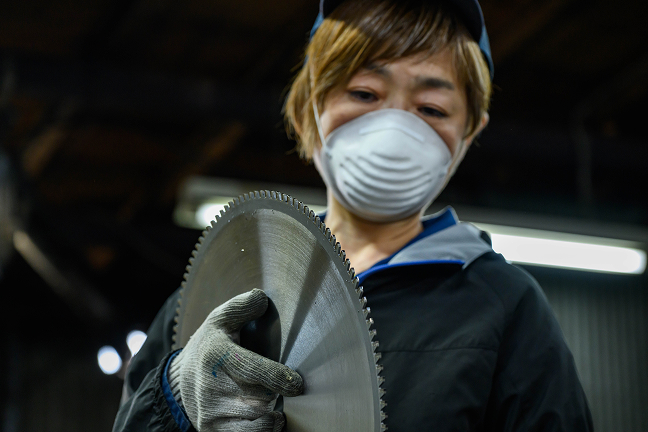
まず、チップが欠けてないかチェックします。
欠けている部分に油性マジックで印を入れます。
みんなが作業に早く取り掛かれるように一目で見て解るよう心がけてます。
お客様の名前、預かった日付、納期、そして、チップの欠け部分に印を書き込んでいます。
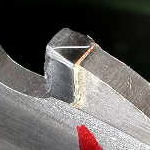
の入ったチップ
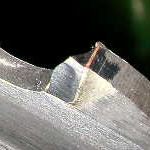
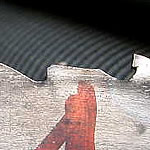
(台金の修理が必要)
② 洗浄
チップソーをきれいに洗浄する工程です。
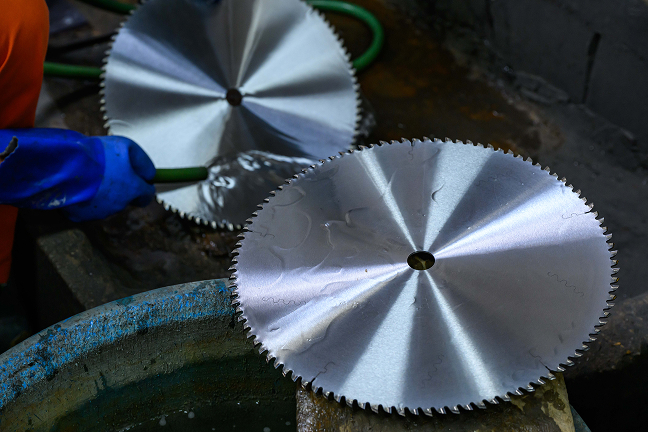
研磨の作業に支障が出てしまいますので、
すべて取り除けるようにきれいに洗浄します。
ときには特別な液体につけて、2,3日かけて洗浄する刃物もあります。
この工程は、主に木工用・樹脂用チップソーに施します。
下処理
アルカリ性の水溶液に漬けて、木のヤニ、樹脂を取り除きやすくします。
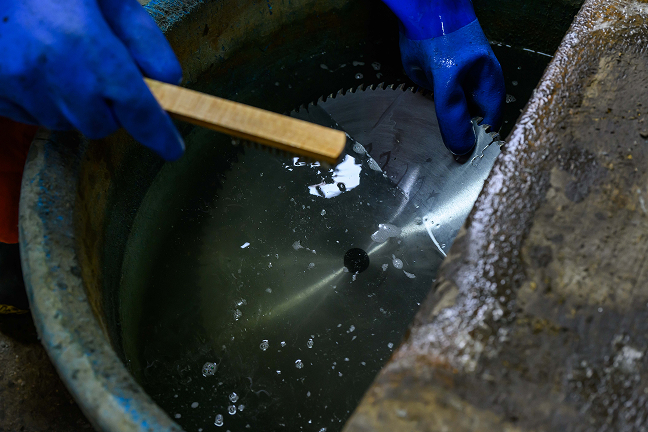
洗浄
ブラシで異物を取り除き、水道水をかけて洗い流します。
ボディや刃の側面に付着した異物を取り除くことにより、研磨向上を図ります。
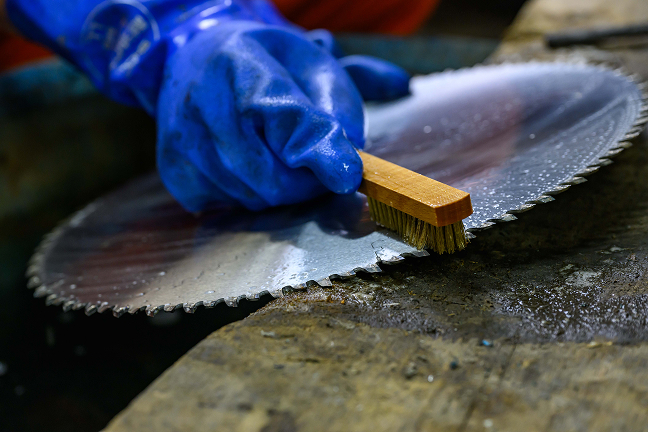
コーティング作業
水道水による錆を防止するため、アルカリ性水溶液でコーティング作業を行います。
③ 台金の整形
刃先から刃底までの深さを適切な状態にするための工程です。
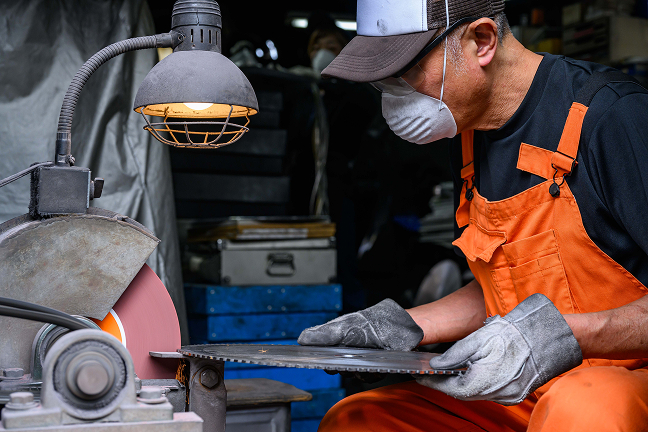
キリコはけの為の作業ですが、しっかり整形することで、
チップがとれにくくなる基礎にもなります。
後の工程のことも考えて、丁寧な作業を心がけています。
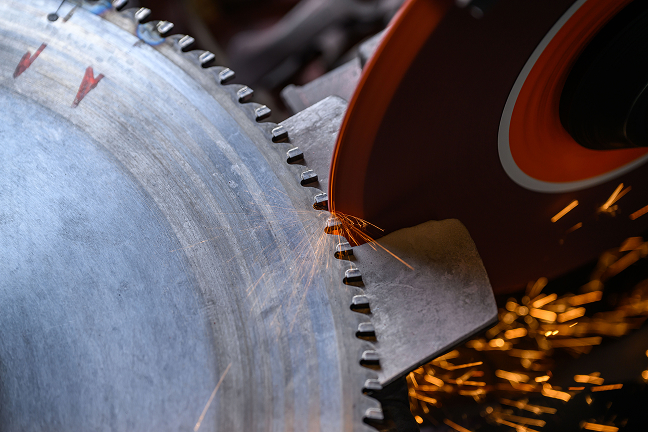
外周研磨の時、クリアランスを確保するために行ないます。
刃先から刃底が深すぎると強度が保てません。
→ 刃が破損することもあります。
刃先から刃底が浅すぎるとキリコが排出できません。
→ 目詰まりの原因になります。
軽切削用
木工、樹脂用etc
台金の切削
クリアランスが0.5mm程度になるように台金を削る作業を行います。
深さの調整
刃から刃底までを適切な深さ(4~5mm)にする作業を行います。
重切削用
鉄、非鉄
強度確保のため、台金背面袋部分の成型が異なります。
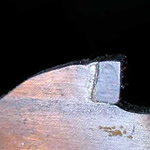
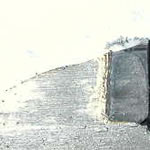
台金修理
破損した台金を再生させるための工程です。
台金ごとチップがかけている場合、台金修理をおこないます。
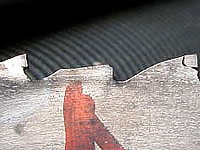
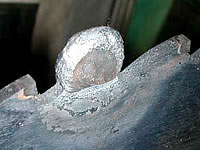
この肉盛り溶接時には、温度管理が重要になります。
温度が低すぎると、「す」が入ったように内部が空洞になり、
もろくなったり、折れたりします。
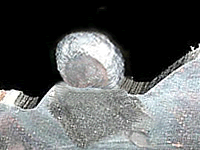
肉盛り溶接の部分にチップがのるよう
ボラゾンホイールで整形
ロー付け
超硬チップを刃先に接合する工程です。
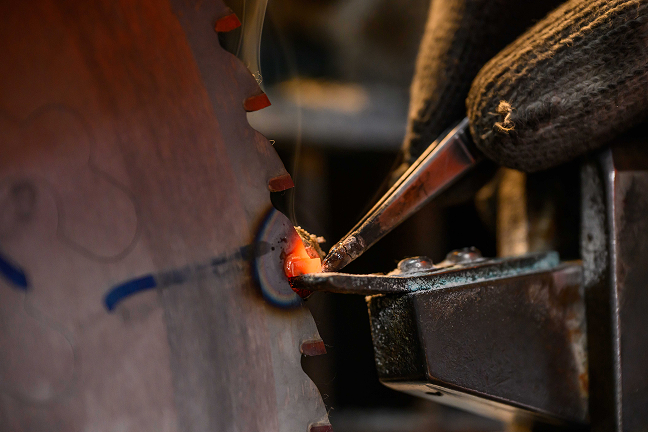
銀ローを溶かす工程では温度管理を“目”で判断します。
真っ赤になるまで焼くのに、一瞬の時間しかかけられません。
時間がかかりすぎると銀が痛んでしまうので、
機械の調整が必要になるからです。
数秒で温度を見極めるので、しっかり集中して作業しています。
不良チップを取り除き、新しいチップを取り付けます。
欠損部分を確認
ルーペを使用し、欠損部分を詳細に確認します。
高周波で加熱
超硬の欠片が残っている場合があるので、高周波で加熱して取り除きます。
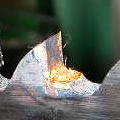
高周波で加熱し、不良チップを除去した部分
研磨作業
高周波の熱で焦げてあれた状態になった部分やシート面をボラゾンホイールで磨いて仕上げていきます。
微少に残った超硬の欠片も取り除くことが出来ます。
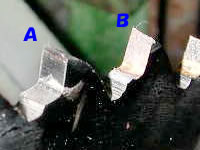
ボラゾンホイールで磨く前後のシート面(チップの乗るところ)
A:磨いた後のシート面
B:磨く前のシート面
角度調整
スクイ面の角度に合わせてシート面の角度を合わせます。
この作業を的確に行うことで、超硬チップをロー付けするときに隙間が無くなり、ロー付けの精度が上がり、チップが長持ちするのです。
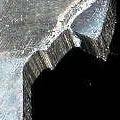
台金修理部分でチップのロー付け前
ロー付け
この作業のポイントはロー付けするチップの温度管理です。
温度が高すぎると超硬チップが割れてしまい、温度が低すぎるとロー付けが出来ません。
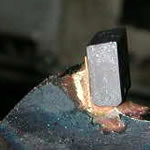
ロー付け
側面研磨
チップの側面のバランスを整える工程です。
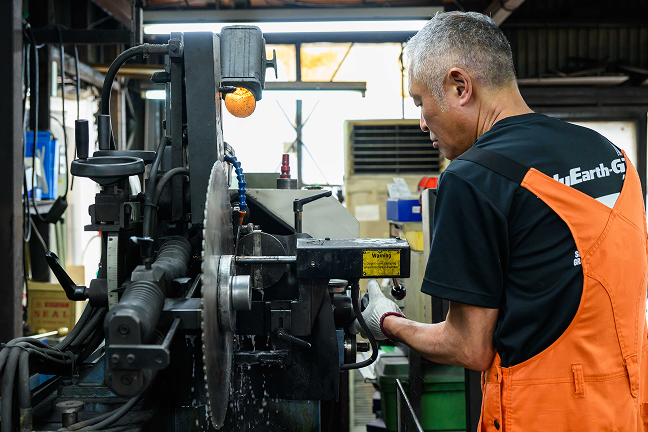
ロー付けで余分に出ている幅を研磨します。
一部分だけ幅が出ていると、その箇所ばかりでしか削れなくなります。
幅が均一になるよう0.01mm単位まで正確に作業しています。
この作業はロー付けした超硬チップと活きている他の超硬チップとのバランスを整える作業です。
側面研磨加工前
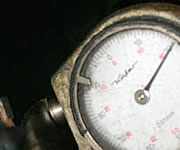
(台金の高さより”0.2”高い)
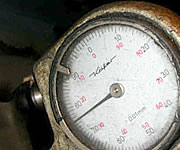
側面研磨加工
ロー付け部分の側面研磨後
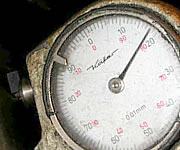
かぎりなくロー付けしていない刃に近づけて、側面誤差”0”にします。
研磨作業は、「側面逃角」と「あさり角」の2つの角度を一度に調整します。
なぜ「側面研磨加工」が必要?
活きている他の超硬チップに触らずに、ロー付けした超硬チップの高さを他の超硬チップに合わせることでチップソーの精度が保てます。
活きている他の超硬チップまで研磨してしまうと、全体のクリアランスが小さくなり、ひどくなると以下の様な現象が現れます。
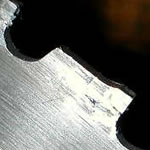
チップの小さい刃
- 切削抵抗が重くなる
- 切断面が焼けたりする
- あさりがなくなるため、刃物の寿命が短くなる
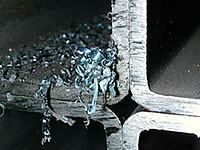
“あさり”のきいていない刃でカットするとこのように、外にキリコがはけなくなり、パイプ内に”かえり”が多く残ります。
④ スクイ面の研磨
刃先の角度を適切な状態にするための工程です。
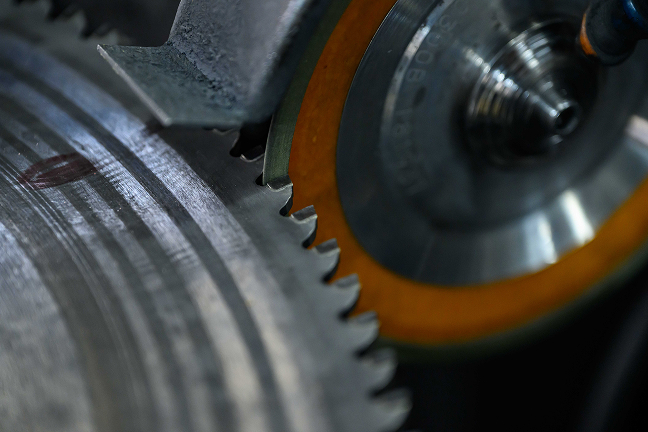
磨り残しが無い様にとにかくフラットにすることが大切です。
規定の角度を保って削ることを気をつけています。
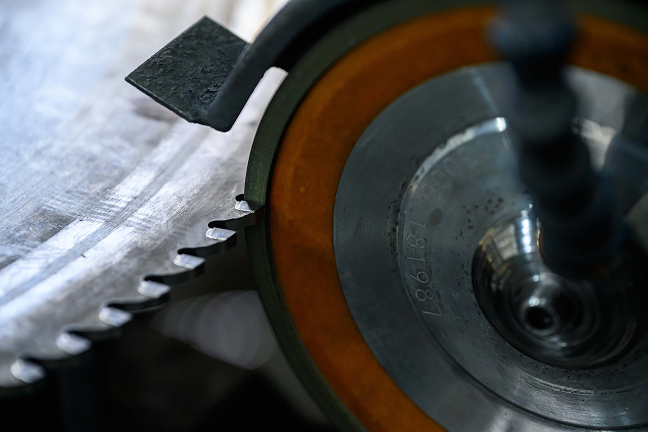
研磨作業は、「スクイ角」と「スクイリード角」の2つを一度に研磨します。
角度を合わせる
材質によって角度が異なります。
材質:鉄 / アルミ / 木工
角度:鈍角 / 鋭角
その角度はメーカー指示適正角度(基準)が定められています。
刃先に刻印されていたり、ケースに書かれているものもあります。
スクイ面の研磨
刃の磨耗部分を取り、切れ味を良くするためスクイ面を研磨します。
刃が磨耗していると、うまく切れない、バリが激しい、切れ味が重い、
切断面が粗いなどの現象が起こります。
材質や機械設備に合わせて最適な台金成型とスクイ面の研磨を行うと3つのメリットが得られます。
- 切削抵抗が軽減されます。
- 刃が長持ちしてランニングコストが軽減できます。
- 仕上がりの切削面がきれいで後加工が軽減されます。
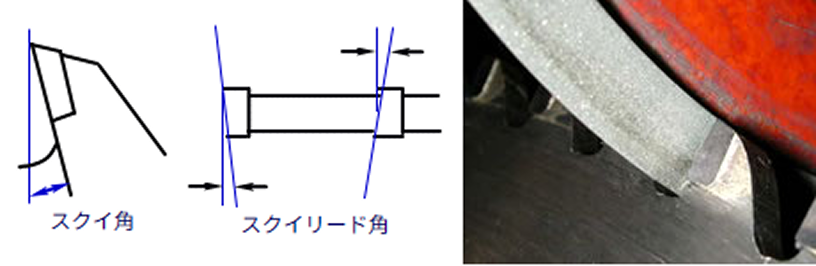
面取りカッター研磨風景
スクイ角・リ-ド角をダイヤモンドホイ-ル(砥石)の面に沿って角度をあわせます。
刃先表面、上下左右が均等にすり合わさっているか再確認!!
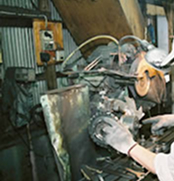
しっかり研削液を掛けながら慎重に磨耗部分を取り除きます。
交互リ-ドであればこの作業を1枚のカッタ-で2度繰り返します。
全ての刃の磨耗を取り除いたら0研削!!これが大切です。
全ての刃が同じ追い込み位置で研磨が仕上がっているかの確認。
その後外周公差等の確認後、刃先保護の為のシ-ルを巻いていよいよお客様の製造現場へ出荷されるのです。
面取りカッター研磨をする前後の比較
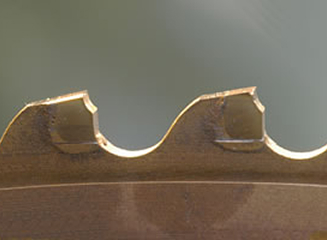
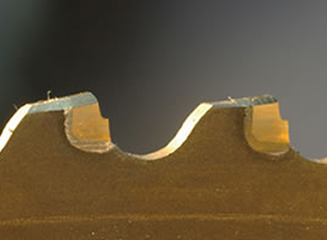
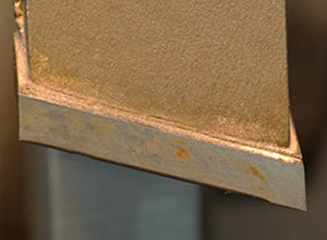
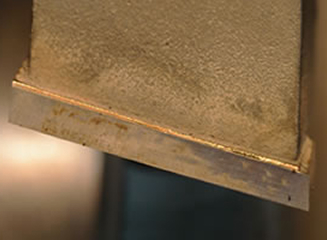
加工前の写真、刃の先端部分が黒くなっているのが判りますか?
これが磨耗部分です。(写真の関係で黒いですが実際には白くなっているものもあります。)
おおよそ0.2~0.3ミリ程磨耗が進んでいます。
加工後の写真では磨耗部分が取り除かれ、左右均等にエッヂが立っている事が判ります。
⑤ 外周研磨
刃先の角度を最適な状態にするための工程です。

CX100という加工機械を導入したことにより加工精度が上がります。
その要因は、サーボモーター制御になったため。
また、いくつもの工程が一度に片付き、仕事が速い!
数もこなせて残業知らずですよ!
機械のチェックを細かく行い、 ミスが無いように操作することに気をつけています。
角度を合わせる
外周逃げ角、研ぎ角を合わせます。
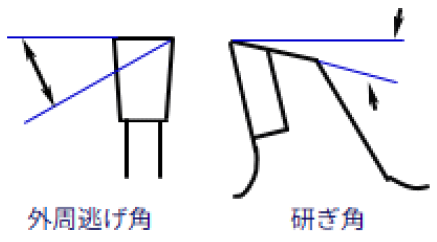
粗研磨
この作業は、摩耗を丁寧に取り除く作業です。
『0.2㎜~0.3㎜』
専用自動機の砥石と当たりしろが接触したときの音を注意しながら作業します。
- 砥石が破損したり消耗が大きくなる可能性がある
- そのため適切な精度が保てない可能性がある
- 外周が正しい円でない可能性がある
- もしくは、何らかの理由で超硬チップがとんでいる可能性がある
0研磨
皮一枚触れている程度の研磨を行い精度ある仕上げにします。
砥石(ダイアモンドホイール)の粗さを変えて研磨を行います。
その結果木工、アルミ、鉄、全般にわたり以下のメリットがあります。
- 刃先端は鏡面に近い仕上がりになり、加工した製品は後加工がとても楽になります。
- 刃のエッジがシャープになるので、切断面の見栄えがとても美しくなります。
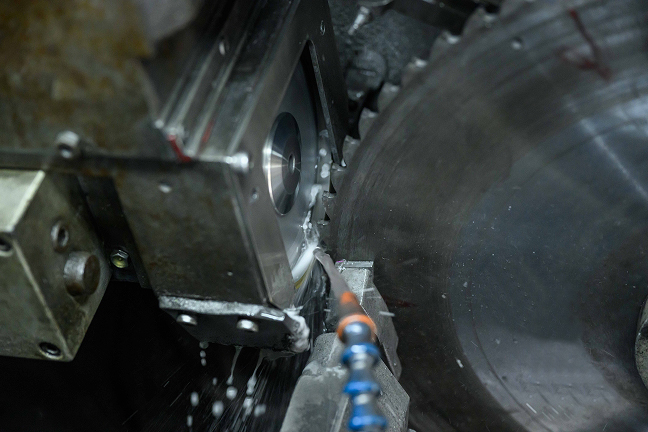
⑥ 外周精度チェック
刃物の外周を均等にするためのチェック工程です。
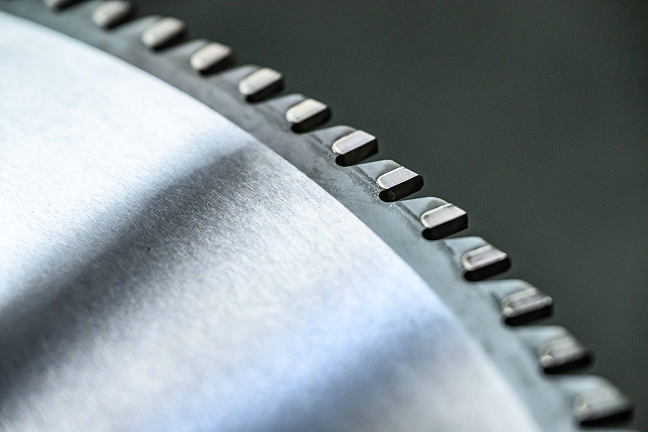
手作業でのチェックになります。
誤差があると前の工程に戻す必要があるので正確にチェックします。
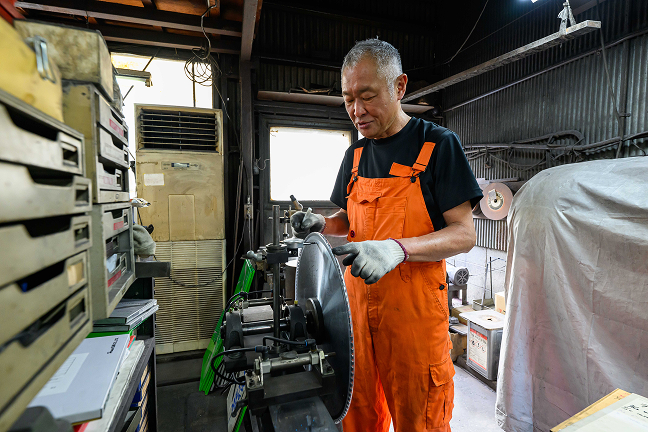
限りなく “0” に近い精度に仕上げるようチェックをします。
ここで、自社開発の改良型オリジナル測定器にて外周を測定します。
誤差:直径 0~100分の3以内にいたします。
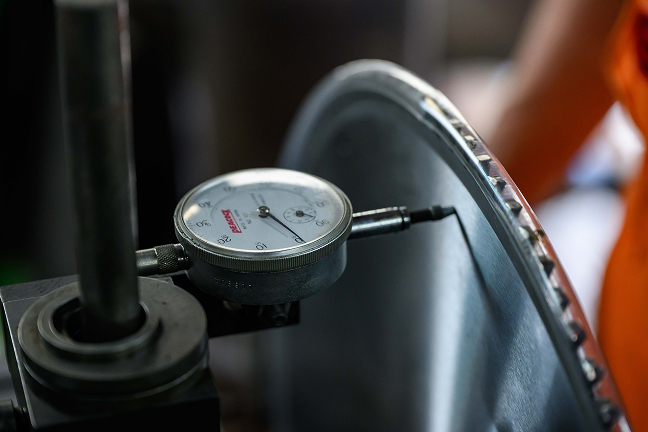
表示の誤差は0.01mm
人間の髪の毛の太さが大体0.01~0.02mmです。
⑦ 腰・歪みチェック・修正
刃物の歪みや腰量を最適な状態にするための工程です。
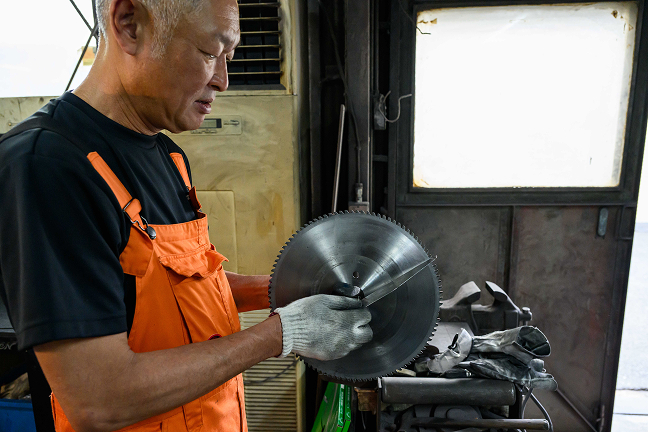
腰と歪みをしっかりと見極めます。
回転の遅い、早いによっても調整が変わってくるんです。
力をしっかりとかける作業で、技術がいる作業です。
切断作業を行うとチップソーに必ず負荷や抵抗が掛かります。
その結果、チップだけではなく、台金・鉄板部分にも影響がでるのです。
目で見て、指で押してチェック
親指を使って台金ボディー2ヶ所に圧力を加えて、感覚で歪みを確認します。
ハンマー修正
作業経験が10年以上の職人技。
熟練工でなくてはできない作業と言われています。
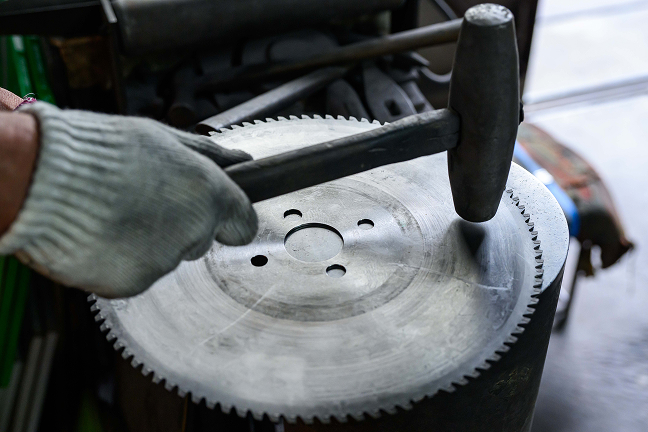
ソートー鋼業では、ロールプレス(社長考案 自社改良型プレス機)を活用して、長年の経験や勘に頼っていた部分をデジタル数値化し、熟練工でなくても均一の精度を保つことができるようにしました。
『腰』のチェック
この作業のポイントは腰量を確保することです。
お客様の作業環境や材質などを考慮して腰の仕上げをしています。
- 腰が硬い(プラス)チップソーに仕上げる
- 腰が抜けている(マイナス)チップソーに仕上げる
腰が硬い・抜けている、歪みがあるという場合には、以下の現象が起こります。
- まっすぐに切れない
- 研磨をきちんとしても切断面がきたない
- 回転中ぶれる
腰・歪みの修正も切断する材質や設備によって異なります。
- 製品を切断する時、抵抗が加わるとチップソーがぶれる
- チップソー自身の柔軟性がない
- チップソー自身に柔軟性がある
- 高速回転するとチップソーがぶれる
2ヶ所にピンポイントで圧力をかけると、
- 腰が硬い(+)= 刃先が下を向く
- 腰が抜けている(-)=刃先が上を向く
なるべく“-”へもっていくのが基本ですが、回転数によって異なります。
腰・歪みの最終チェック
感覚ではなく、数値で表せるので安定した仕上がりを保証。
自社の経験と実績、チップソー専門メーカーの協力によりデータ化を実現しました。
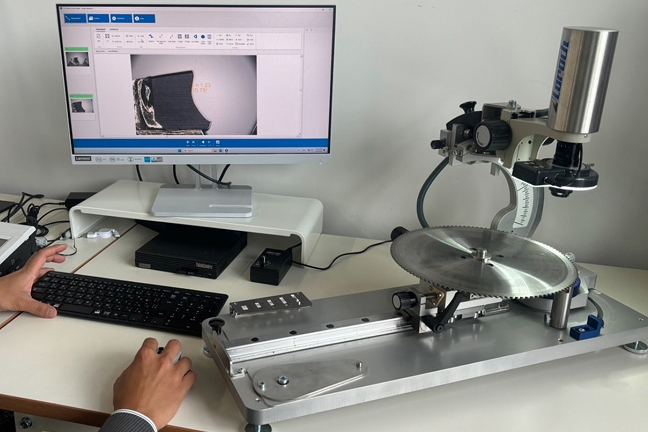
⑧ 仕上げ作業
研磨加工済みの刃物をきれいな状態でお届けするための工程です。
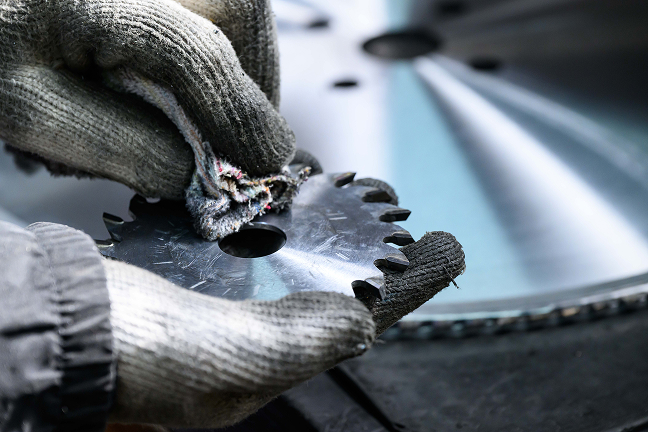
みんなが丁寧に研磨してくれた刃物です。
刃が欠けないようにテープを巻いて、きれいにふいて仕上げるのが私の仕事です。
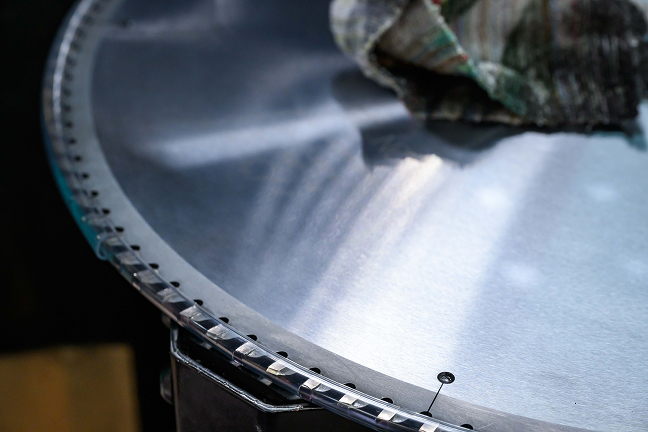
シンナーと特殊ワックスで磨き、錆び止め、保護、ツヤだしを行い、刃先保護テープをつけて出荷します。